The Ultimate Guide to Industrial Blade Factories: Quality, Precision, and Services
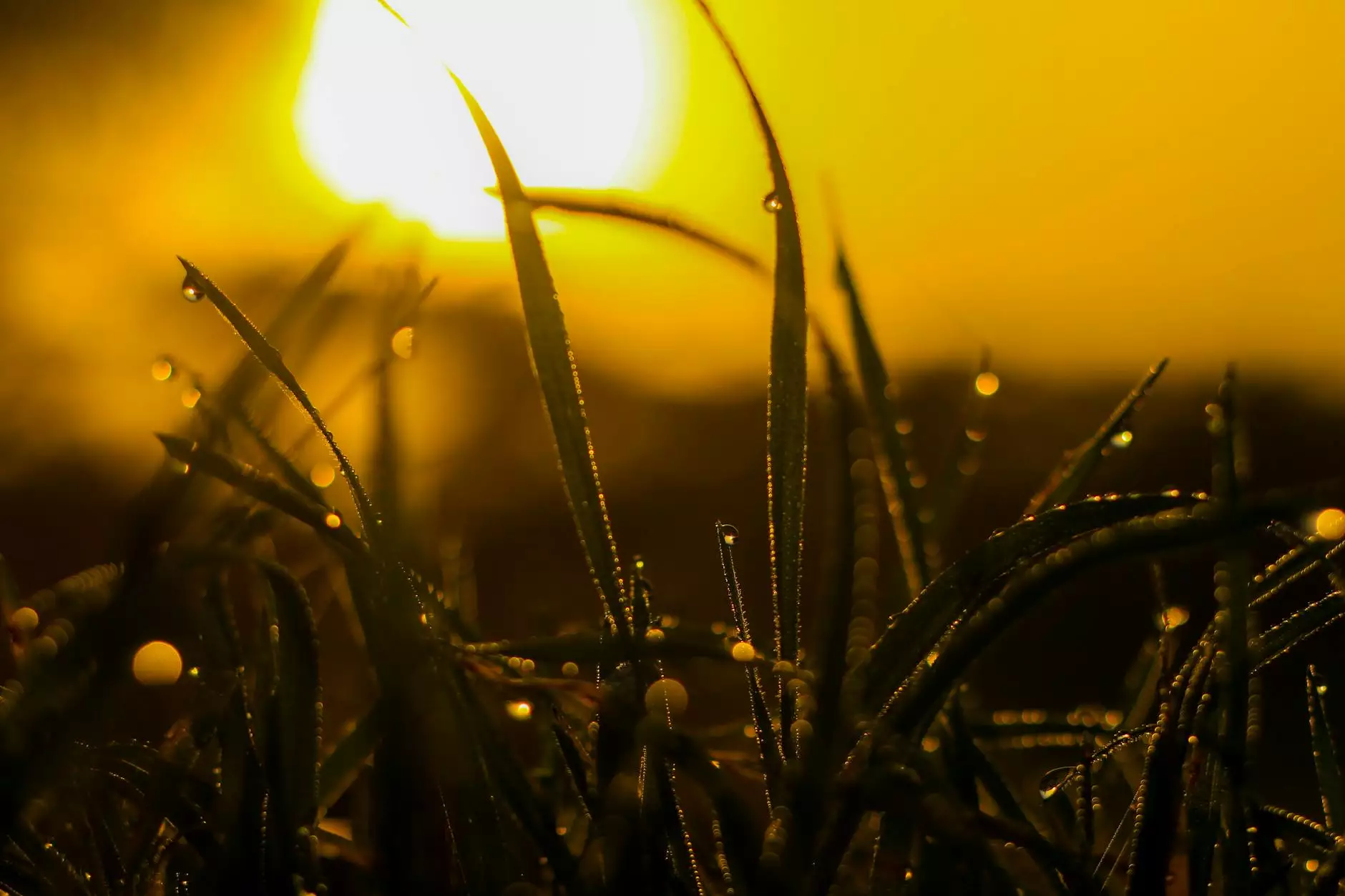
The realm of industrial blade factories represents a critical sector in manufacturing that powers countless industries. From food processing to metalworking, the demand for robust, reliable blades is paramount. This article dives deep into the operations, significance, and innovations surrounding industrial blade manufacturing, specifically tailored for businesses seeking expertise in knife sharpening and professional services. Discover how companies like szblade.com are leading the way in quality and service excellence within this vital field.
The Importance of Industrial Blade Factories
Industrial blades are essential tools used in various applications. The craftsmanship involved in producing these blades not only contributes to prolonged equipment life but also enhances operational efficiency. Here, we explore why industrial blade factories are indispensable for several industries:
- Enhanced Productivity: Quality blades ensure that machines operate efficiently, reducing downtime due to maintenance.
- Precision Cutting: Superior blade design and manufacturing lead to cleaner cuts, which can significantly reduce waste in processes.
- Cost-Effectiveness: High durability of industrial blades minimizes the frequency of replacements, providing long-term savings.
- Versatility: A variety of blades can be designed for specific applications, catering to diverse industrial needs.
- Innovation: Continuous advancements in blade manufacturing technologies pave the way for smarter, more effective tools.
Understanding the Manufacturing Process in an Industrial Blade Factory
The manufacturing process of blades in an industrial blade factory involves several critical steps, each contributing to the final product's quality and effectiveness:
1. Material Selection
The backbone of any quality blade is its material. High-carbon steel, stainless steel, and carbide are common materials selected for their durability and cutting performance. The selection process focuses on:
- Strength: The material must withstand high stress and temperature.
- Corrosion Resistance: Essential for blades that come into contact with moisture.
- Edge Retention: The ability to maintain sharpness over prolonged use.
2. Blade Design
Blade design is pivotal in determining performance. Engineers create detailed specifications using computer-aided design (CAD) software. Considerations include:
- Shape and Size: Tailored to meet the specific cutting needs of various materials.
- Tooth Configuration: Optimized for cutting efficiency and material type.
- Weight Distribution: Ensures balanced handling during operation.
3. Manufacturing Techniques
Modern manufacturing employs various techniques to create blades, including:
- Forging: Involves shaping metal using localized compressive forces, resulting in strong, ductile blades.
- Laser Cutting: Precision cutting that allows for intricate designs and high accuracy.
- Grinding: Ensures the blade's edge is sharpened to perfection, crucial for performance.
4. Quality Control
Before reaching the market, blades undergo rigorous quality control processes. These tests ensure:
- Durability Testing: Evaluates how well blades withstand stress and usage.
- Sharpness Testing: Measures the effectiveness of the blade's edge.
- Material Integrity Checks: Assures that the materials meet required specifications.
Expanding Services: Knife Sharpening and Professional Services
In addition to manufacturing, industrial blade factories often provide essential services such as knife sharpening and other professional services. Let’s explore these offerings in detail:
Knife Sharpening
Maintaining blade sharpness is crucial for optimal performance. Professional knife sharpening services include:
- Precision Sharpening: Using advanced equipment to achieve the perfect edge angle.
- Burr Removal: Ensuring that no imperfections disrupt cutting efficiency.
- Custom Sharpening Solutions: Tailored services depending on blade type and use case.
Maintenance Programs
Regular maintenance is key to prolonging the life of industrial blades. Factories often offer programs that include:
- Scheduled Inspections: Regular checks to determine the blade's condition.
- Repair Services: Addressing damages and restoring blade functionality.
- Performance Optimization: Adjusting blades based on their usage patterns for improved efficiency.
Technological Innovations in Blade Manufacturing
The world of industrial blade manufacturing is continuously evolving, thanks to technological advancements. Here are some of the most exciting innovations:
1. Automated Manufacturing Processes
Automation in blade manufacturing has resulted in higher precision, reduced waste, and improved safety. With robotics handling repetitive tasks, factories can:
- Increase Efficiency: Streamlining production processes.
- Enhance Consistency: Reducing human error in manufacturing.
2. Smart Blades
Emerging technologies have led to the development of smart blades equipped with sensors that monitor performance metrics. These can include:
- Real-Time Usage Data: Allowing for predictive maintenance.
- Performance Feedback: Providing insights for optimization.
3. Sustainable Manufacturing Practices
In response to global environmental concerns, many industrial blade factories are adopting sustainable practices. This includes:
- Recycling Materials: Utilizing scrap metal to create new blades.
- Energy Efficiency: Implementing energy-efficient machinery to minimize carbon footprints.
The Future of Industrial Blade Factories
The future for industrial blade factories is bright, driven by innovative technologies and evolving consumer demands. Factors influencing this growth include:
1. Expanding Market Demand
Across various industries, the need for high-quality industrial blades continues to grow. Particularly in sectors like:
- Food Processing: Increased demand for precision cutting tools.
- Automotive Manufacturing: Needs for sharp, reliable cutting tools for component fabrication.
2. Emphasis on Customization
As industries evolve, the desire for customized blades that meet specific operational needs increases. This drives innovation in blade design and manufacturing processes.
3. Integrating AI and Data Analytics
The integration of artificial intelligence in production and maintenance allows for enhanced decision-making. Data analytics can lead factories to:
- Streamline Operations: Based on performance data.
- Enhance Product Development: Using insights to innovate blade designs.
Conclusion
In summary, industrial blade factories play a pivotal role in the manufacturing ecosystem. Their commitment to quality, precision, and advanced technology ensures that industries have the reliable tools they need for success. Whether through professional services like knife sharpening or cutting-edge manufacturing processes, companies such as szblade.com exemplify the future of blade production and service excellence.
Staying informed about innovations in blade manufacturing and maintenance is vital for any business relying on industrial cutting tools. By choosing reputable industrial blade factories, companies can significantly enhance their productivity and operational efficiency.