Understanding Injection Mold Tools: Revolutionizing Metal Fabrication
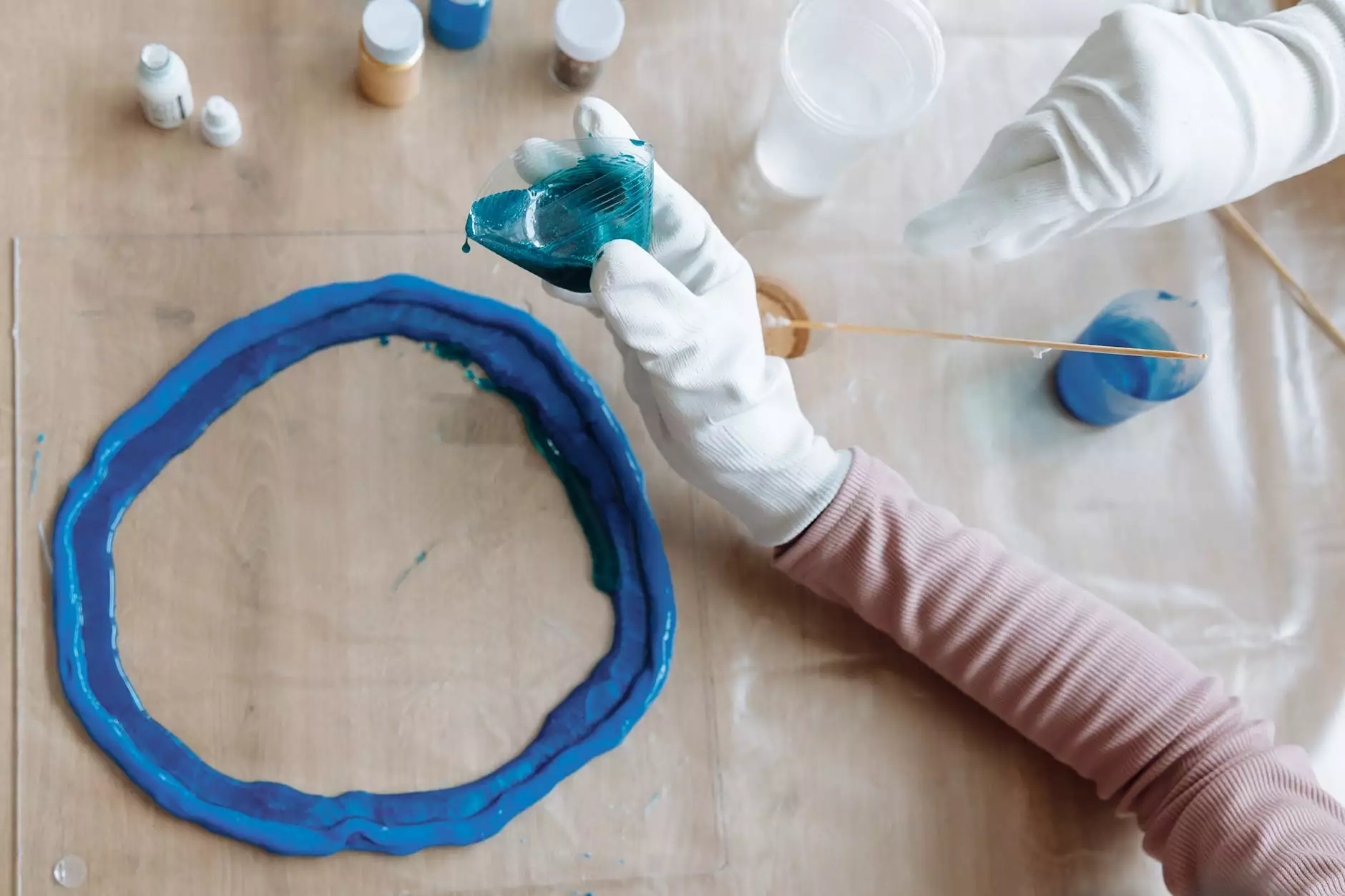
Injection mold tools represent a cornerstone of modern manufacturing, particularly in the realm of metal fabrication. The precision and efficiency these tools bring to the table have transformed how parts and components are produced in various industries. This article aims to explore the fundamentals of injection mold tools, their applications, and their significance in revolutionizing the manufacturing landscape.
The Basics of Injection Mold Tools
Injection molding is a manufacturing process used to produce parts by injecting molten material into a mold. While primarily associated with plastics, the principles of injection molding extend to metal components, thanks to advancements in technology. Injection mold tools are the backbone of this process, allowing for the consistent and repeatable production of intricate designs.
- Types of Injection Molding: The main types include normal injection molding, multi-shot injection molding, and gas-assisted injection molding.
- Materials Used: Common materials include thermoplastics, thermosetting plastics, and metals like aluminum and magnesium.
- Applications: Industries such as automotive, aerospace, electronics, and consumer goods extensively utilize injection mold tools.
How Injection Mold Tools Work
The process begins with material selection. Depending on the intended application and required properties, manufacturers may choose to work with a variety of materials such as steel, aluminum, or synthetic polymers. Once the material is selected, it undergoes a series of preparation steps, including:
- Material Melting: The raw material is heated until it becomes molten.
- Mold Filling: The molten material is injected into the mold at high pressures, filling every intricate detail of the mold cavity.
- Cooling: The material is allowed to cool and solidify, taking the shape of the mold.
- Mold Opening: Once cooled, the mold opens, and the finished part is ejected.
The Significance of Precision in Injection Mold Tools
In the world of manufacturing, precision is paramount. Components must fit together seamlessly to ensure functionality and safety. Injection mold tools play a crucial role in achieving this level of precision. They are designed with tight tolerances to ensure:
- Minimal variation between parts.
- High-quality surface finishes.
- Durability under operational stresses.
The intricate design of these tools necessitates the expertise of skilled engineers and designers who understand the nuances of material behavior, thermal dynamics, and structural integrity.
Innovations in Injection Mold Tool Design
Innovation drives the manufacturing industry forward, and injection mold tools are no exception. Advances in computer-aided design (CAD) and computer-aided manufacturing (CAM) have enhanced design capabilities. These technologies facilitate:
- Rapid Prototyping: Engineers can create prototypes in a fraction of the time it used to take, allowing for quicker evaluations and revisions.
- Complex Geometries: Modern tools can produce increasingly complex shapes that were once thought impossible.
- Simulation: Virtual simulations help forecast potential issues in the manufacturing process before production begins.
Material Selection in Injection Molding: A Critical Factor
The choice of material is a critical determinant of the performance of market products. Key aspects to consider include:
- Mechanical Strength: Depending on the application, materials must withstand specific loads and stresses.
- Temperature Resistance: Some applications may require materials that can endure high temperatures without deformation.
- Corrosion Resistance: In environments exposed to chemicals, the choice of a corrosion-resistant material is vital.
For instance, injection mold tools made from high-grade steel might be utilized for automotive parts, while aluminum might be chosen for lightweight consumer products.
Quality Control in Injection Mold Tools Manufacturing
Quality control is integral to the injection molding process. To ensure that parts meet the rigorous standards demanded by industries, manufacturers must implement stringent testing and quality assurance protocols. These may include:
- Dimensional Inspection: Verifying that the dimensions of the produced parts fall within acceptable limits.
- Material Analysis: Ensuring the correct material properties are achieved and maintained.
- Functional Testing: Testing parts under real-world conditions to guarantee performance.
The Advantages of Using Injection Mold Tools
Utilizing injection mold tools comes with a host of advantages that can significantly benefit manufacturing processes:
- Efficiency: Large quantities of parts can be produced quickly and consistently.
- Cost-Effectiveness: While the initial investment in molds can be high, the cost per part decreases significantly with large runs.
- Flexibility: Molds can be designed for various products, allowing manufacturers to pivot quickly based on market demands.
How DeepMould.net Utilizes Injection Mold Tools
At DeepMould.net, we are committed to leveraging the latest advancements in injection mold technology to enhance our metal fabrication services. Our approach includes:
- State-of-the-Art Facilities: Equipped with the latest injection molding machines and technologies.
- Expert Engineers: Our team consists of highly trained professionals who specialize in mold design and fabrication.
- Customized Solutions: We offer tailored services that meet the specific needs of our clients across various sectors.
Environmental Considerations in Injection Molding
As sustainability becomes a focal point in manufacturing, injection mold tools have also evolved to incorporate environmentally friendly practices. Efforts include:
- Material Recycling: Utilizing recycled materials to reduce waste and environmental impact.
- Energy Efficiency: Investing in energy-efficient machinery that decreases overall energy consumption.
- Waste Minimization: Implementing practices to minimize scraps and improve overall efficiency in production.
The Future of Injection Mold Tools
The future of injection mold tools looks promising, with rising trends such as 3D printing complementing traditional manufacturing techniques. The integration of smart technology, including sensors and IoT devices, will pave the way for:
- Enhanced Monitoring: Real-time monitoring of the production process to ensure quality and efficiency.
- Predictive Maintenance: Utilizing data analytics to predict equipment failures before they occur.
- Customization at Scale: Providing customization options quickly without sacrificing production speed.
Conclusion
In summary, injection mold tools are revolutionizing the metal fabrication industry, offering a plethora of benefits from precision to cost-effectiveness. As technology continues to evolve, the role of these tools will only become more significant. Manufacturers looking to improve their production processes must understand and leverage the capabilities of injection mold tools to stay competitive in today’s fast-paced market.
For more information and to explore our services, visit DeepMould.net, where we dedicate ourselves to providing high-quality metal fabrication services that incorporate the best practices in injection molding technology.