Plastic Prototype Manufacturing: The Future of Product Development
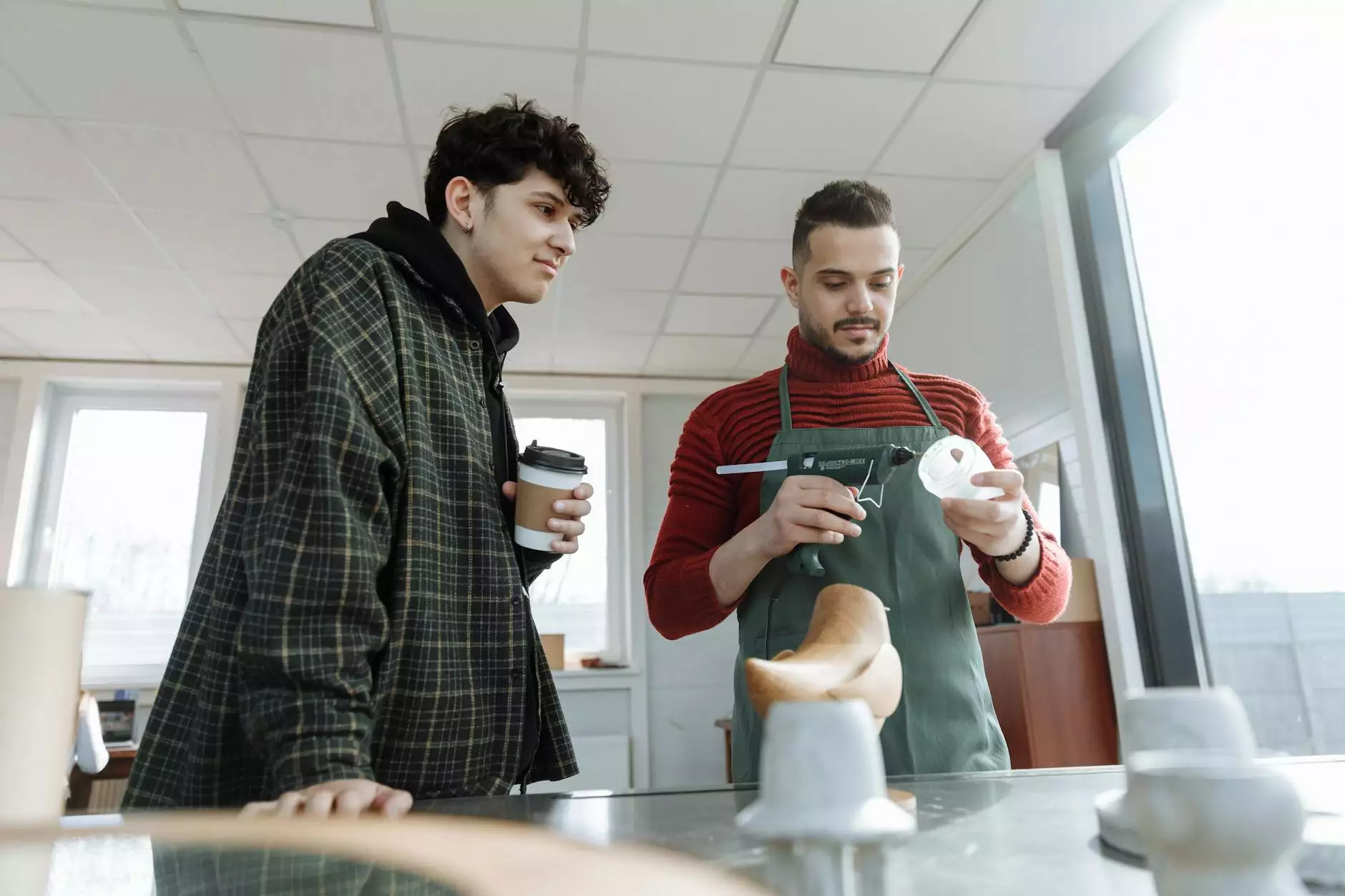
The landscape of plastic prototype manufacturing is evolving at an incredible pace. This innovation is crucial for businesses that want to stay ahead in today’s competitive market. From startups to established enterprises, understanding and leveraging modern manufacturing techniques can lead to significant advantages.
Understanding Plastic Prototype Manufacturing
Plastic prototype manufacturing involves the creation of prototypes using various types of plastic materials. These prototypes are critical in the product development process, allowing designers and engineers to test their concepts in the real world. By utilizing advanced manufacturing methods, businesses can reduce costs while improving product quality and time-to-market.
The Importance of Prototyping in Business
Prototyping is not just a step in the design process; it’s an essential phase that can make or break a product launch. Here are several reasons why prototyping holds immense value in business:
- Risk Reduction: Prototypes help identify design flaws before mass production, reducing the risk of costly changes later.
- Enhanced Communication: A physical prototype aids discussions between teams, stakeholders, and potential investors, offering a tangible reference.
- Market Validation: Prototypes can be used to gather consumer feedback, validating whether an idea is viable before full-scale production.
- Iteration and Refinement: They allow for testing and iterative improvement based on real-world use cases.
Advancements in Plastic Prototype Manufacturing
The advancement of plastic prototype manufacturing has been propelled by several cutting-edge technologies. This section will delve into the most critical innovations that are shaping the industry.
1. Additive Manufacturing (3D Printing)
3D printing has revolutionized the way prototypes are made. This process allows for:
- Rapid Production: Create prototypes in hours instead of weeks.
- Complex Shapes: Achieve designs that are impossible to fabricate using traditional methods.
- Material Variety: Utilize different plastic materials tailored for specific applications.
2. CNC Machining
Computer Numerical Control (CNC) machining allows for highly accurate and consistent prototypes. Key benefits include:
- Precision: Ensures prototypes meet exact specifications.
- Durability: Produces sturdy components suitable for function testing.
- Versatility: Compatible with a wide range of plastics and finishes.
3. Injection Molding
While traditionally thought of for mass production, injection molding is increasingly used for prototyping as well. Advantages of this method include:
- High Volume: Ideal for producing multiple prototypes rapidly.
- Surface Finish: Offers superior surface quality and details.
- Material Efficiency: Minimizes waste during the production process.
Choosing the Right Method for Your Needs
When it comes to plastic prototype manufacturing, selecting the right production method depends on various factors:
- Project Scale: Is this a one-off prototype or do you need multiple iterations?
- Precision Requirements: How tight are your tolerances for the prototype?
- Material Properties: What type of plastic is best suited for your application?
- Time Constraints: How quickly do you need the prototype completed?
Benefits of Plastic Prototypes
Utilizing plastic prototypes offers numerous benefits that can significantly enhance product development:
- Cost-Efficiency: Early-stage prototyping helps save on costs that come from late-stage modifications.
- Design Flexibility: Quickly iterate on designs based on feedback and testing.
- Enhanced Collaboration: Foster better teamwork by using physical models as focal points for brainstorming and testing.
- Faster Time to Market: Streamlined prototyping processes reduce development timelines.
Real-World Applications of Plastic Prototypes
The applications of plastic prototype manufacturing span across numerous industries, showcasing its versatility:
1. Automotive Industry
In automotive design, prototypes are essential for testing everything from body panels to intricate interior components. Quick iterations can lead to better designs and safer vehicles.
2. Consumer Electronics
With rapid changes in technology, companies in the electronics space rely on prototypes to test new devices and user interfaces. User experience can be drastically improved through iterative feedback.
3. Healthcare
Medical device manufacturers use plastic prototyping to create ergonomic tools and instruments. Prototyping ensures compliance with stringent health regulations and functional efficacy.
4. Aerospace
Aerospace companies utilize lightweight plastic prototypes to test design concepts that meet safety standards while maximizing performance.
The Future of Plastic Prototype Manufacturing
The future of plastic prototype manufacturing is bright, with exciting trends emerging:
- Sustainability: Eco-friendly materials are becoming more mainstream as companies aim for greener processes.
- Integration of AI: Artificial Intelligence is set to optimize design processes and production efficiency.
- More Advanced Materials: Ongoing research into new plastics will improve performance and reduce costs.
- Technological Convergence: Combining various manufacturing technologies to create even more versatile production solutions.
Conclusion
In summary, the realm of plastic prototype manufacturing is not only about creating models; it’s about transforming ideas into tangible, testable products. By understanding and adopting the latest manufacturing techniques, businesses can significantly enhance their product development process, resulting in faster market entry and a competitive edge.
At Deep Mould, we are dedicated to providing top-tier prototyping services tailored to your specific needs. Let us help you turn your innovative ideas into reality through effective plastic prototype manufacturing today!