Understanding Boiler Water Chemical Treatment
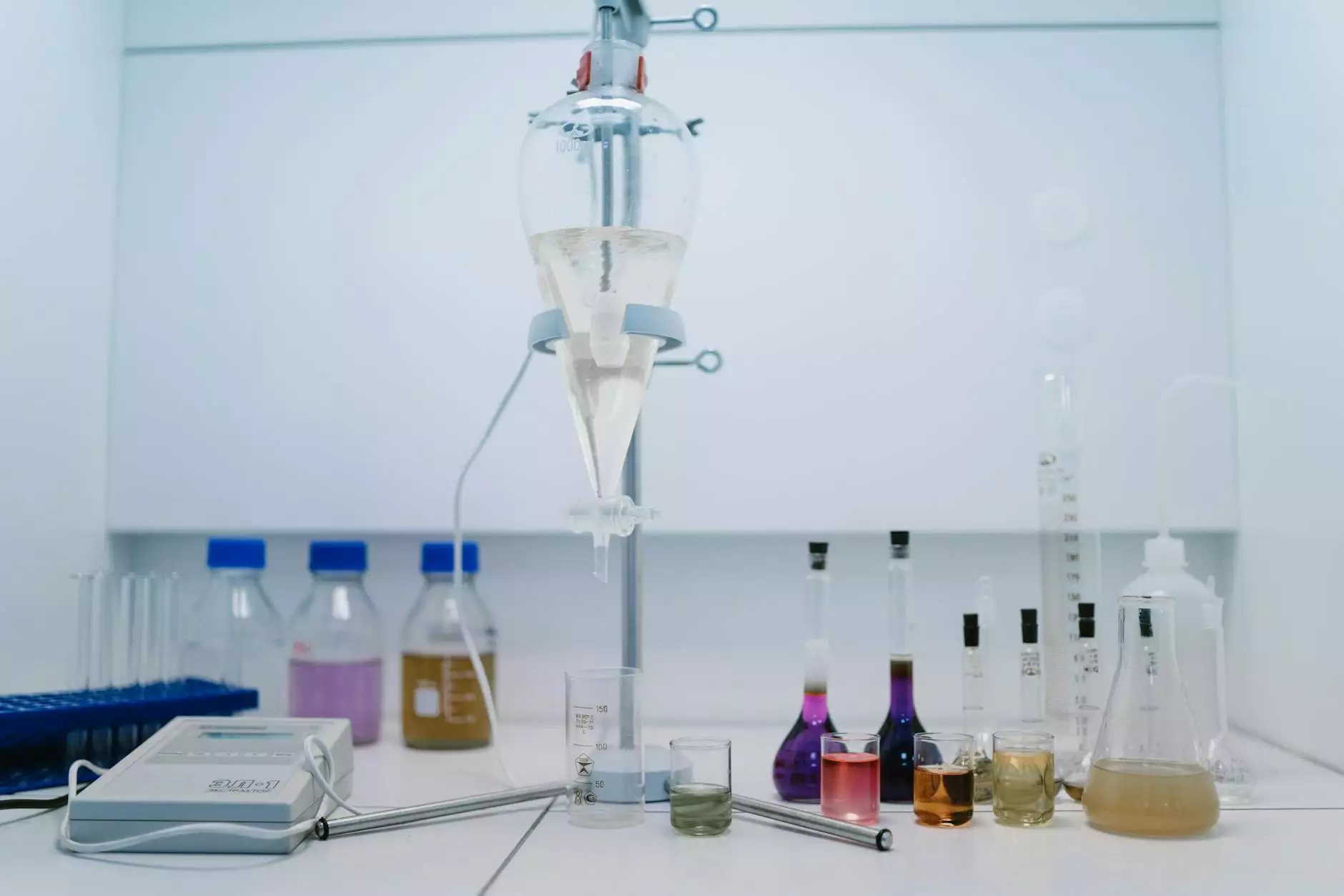
In today’s industrial landscape, the effective management of boiler systems is critical for operational efficiency. Boiler water chemical treatment plays a key role in safeguarding these systems. This comprehensive guide aims to provide valuable insights into the importance, methods, and best practices of boiler water chemical treatment.
What is Boiler Water Chemical Treatment?
Boiler water chemical treatment involves the use of chemicals to maintain the quality of water in boiler systems. Its primary objective is to prevent scale formation, corrosion, and other damaging effects that can compromise boiler performance and longevity. Proper treatment not only enhances the efficiency of the boiler but also reduces operational costs.
The Importance of Proper Boiler Water Treatment
Why is boiler water treatment vital? Here are several key reasons:
- Corrosion Prevention: Corrosion is one of the major causes of boiler failures. Implementing a proper chemical treatment program helps neutralize corrosive elements in the water, significantly extending the life of the boiler.
- Scale Control: The formation of scale deposits can severely affect heat transfer efficiency. By managing hardness and total dissolved solids, boiler water chemical treatment minimizes scale formation.
- Efficient Operation: Treated boiler water ensures optimal thermal conductivity, meaning the boiler operates more efficiently, consuming less fuel.
- Safety: A well-maintained boiler system reduces the potential for hazardous failures, ensuring a safer working environment.
- Cost Reduction: By extending the life of boiler equipment and preventing costly repairs, chemical treatment ultimately leads to reduced operational costs.
Common Challenges Faced in Boiler Operations
Every boiler system faces its unique set of challenges. Understanding these challenges is essential for implementing effective boiler water chemical treatment.
- Scale Formation: Hard water contains calcium and magnesium ions that precipitate and form scale within the boiler.
- Corrosive Elements: Certain gases, such as oxygen and carbon dioxide, can lead to rapid corrosion if not adequately controlled.
- Variable Water Quality: Fluctuations in the source water quality can pose challenges in maintaining optimal boiler water conditions.
- Purge Water Management: Properly handling blowdown and purge water is crucial to minimize water loss and ensure environmental compliance.
Effective Chemical Treatments for Boiler Water
Several chemical agents are commonly used in boiler water chemical treatment. Understanding these is crucial for choosing the right blend for your operations.
1. Oxygen Scavengers
Oxygen scavengers are chemicals used to remove dissolved oxygen from water. Oxygen is highly corrosive, and its presence in boiler water can lead to rapid deterioration of metal components. Common oxygen scavengers include:
- Sodium Sulfite: It reacts with oxygen to form harmless sodium sulfate, effectively eliminating corrosive oxygen.
- Hydrazine: Known for its effectiveness in high-temperature applications, hydrazine serves as a potent oxygen scavenger.
2. pH Control Agents
Maintaining an optimal pH level is essential for minimizing corrosion and scale formation. Common pH control agents include:
- Sodium Hydroxide (Caustic Soda): Adds alkalinity to the water, ensuring a favorable pH level.
- Sodium Bicarbonate: Often used to moderate pH levels, especially in low-pressure boiler systems.
3. Scale Inhibitors
Scale inhibitors prevent the formation of mineral deposits that can compromise boiler efficiency. They work by conditioning the water and altering the crystallization of scale-forming minerals. Examples include:
- Phosphonates: They help disperse scale-forming agents and inhibit their growth.
- Polyacrylic Acid: Acts as a dispersant, effectively keeping minerals in suspension and preventing scale.
4. Anti-Foaming Agents
Excessive foaming within boilers can hinder heat transfer efficiency and cause operational problems. Anti-foaming agents help mitigate this issue. Common choices include:
- Silicone-based agents: Known for their effective foam control properties in high-temperature systems.
- Mineral Oil-based agents: Provide a cost-effective solution for controlling foam in various applications.
Best Practices for Boiler Water Chemical Treatment
Implementing effective boiler water chemical treatment requires adhering to best practices. Here are some guidelines to ensure success:
1. Regular Water Testing
Conducting regular water tests allows for monitoring chemical levels and overall water quality. Testing for pH, conductivity, dissolved solids, and corrosive elements is critical for timely intervention.
2. Continuous Monitoring
Implement continuous monitoring systems to track boiler performance metrics. These systems help in identifying potential issues before they escalate into significant problems.
3. Proper Chemical Dosing
Chemicals should be added in the right concentrations to avoid both overdosing and underdosing. Automated dosing systems can help in maintaining consistent treatment levels.
4. Training Personnel
Ensure that all personnel involved in boiler maintenance and operations are properly trained in chemical handling and safety protocols.
Conclusion
Boiler water chemical treatment is a cornerstone of effective boiler operation in industrial settings. By understanding the importance of treatment, employing effective chemical strategies, and adhering to best practices, organizations can enhance boiler performance, reduce costs, and prolong equipment lifespan. Implementing these strategies will provide significant benefits across the entire operational spectrum.
By partnering with experienced providers like Bimak Skimya, businesses can achieve optimal boiler water quality and overall system efficiency, paving the way for success in their respective industries.